Youth and the increasingly green Canadian automotive industry
For over a century, the automobile was simply regarded as a means to an end. Its job was to get passengers from one place to another, in comfort and safety, in the shortest possible time.
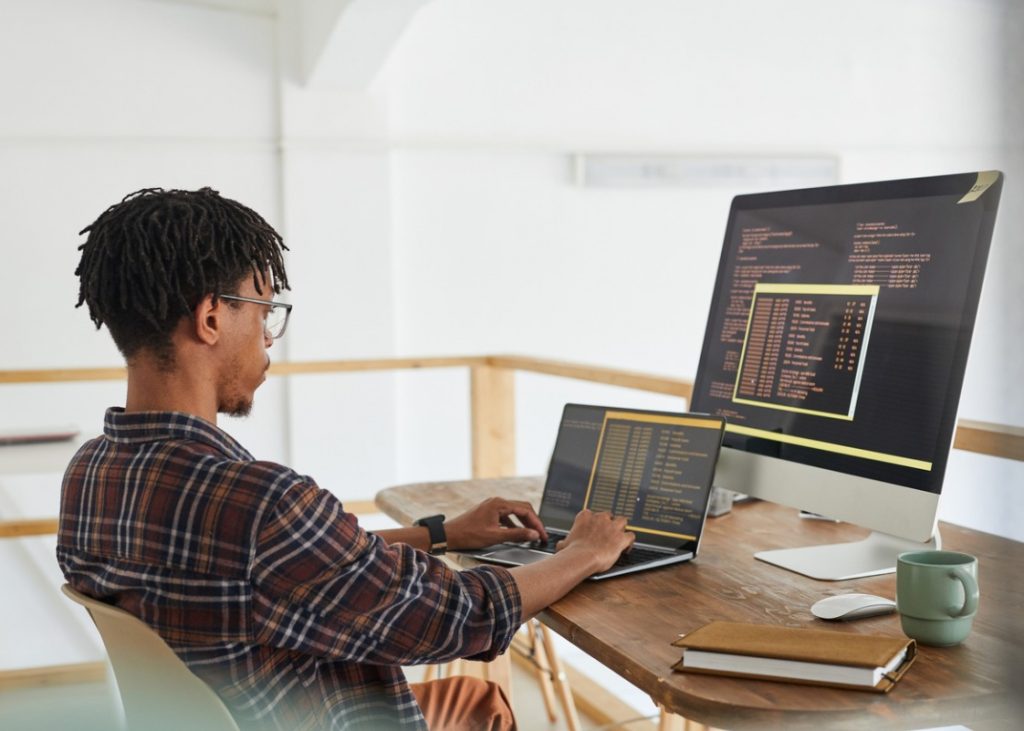
The automobile stood alone. It was a machine in a garage, which we switched on and off and drove around in as circumstances required.
All this has changed – quite dramatically in recent years – and now the cars we drive are increasingly connected to their surroundings.
Several technologies implemented to assist pilots navigate aircraft have already been integrated into automotive features. These include adaptive cruise control, satellite navigation, parking automation, collision avoidance, lane departure assist, automatic lane centering and more.
Today’s cars are computers on wheels
Put another way, the technological innovations that power the automobile of today make them less like the motor car our parents drove and more like computers on wheels.
This emerging reality is impacting the way cars are manufactured and the kind of roles needed to manufacture them.
As we state in our recent report Automotive Industry Labour Market Analysis: Automotive Technology Labour Market Outlook:
“Technology has long played a critical role in the development and production of motor vehicles by Canada’s automotive industry. The importance of automotive technology has only grown in recent years as investments in new areas of innovation, such as autonomous vehicles and hydrogen fuel cells, promise to revolutionize traditional aspects of transportation.”
The new reality of the automobile industry
Whether the car is an all-electric vehicle (EV), a fuel cell electric vehicle (FCEV), a hybrid electric vehicle (HEV), a plug-in hybrid electric vehicle (PHEV), or one driven by a conventional internal combustion engine (ICE), according to Policy Options, Institute for Research on Public Policy:
“The new reality of the automotive industry is seeing an increased demand for well-trained engineering and technical workforces, specializing in robotics, AI, sensors, telecommunications, new materials and advanced manufacturing processes.”
As Policy Options elaborates: “Take, for example, automotive service technicians. Today’s cars run on a complex mix of on-board computers and mechanical components. With the explosion in popularity of electric cars and impending availability of autonomous vehicles, the knowledge and skills needed by tomorrow’s technicians will be even greater.
Technicians will be part of multidisciplinary teams that can update a car’s software over Wi-FI, understand car-to-car (V2V) or can-to-everything (V2X) wireless communication, and integration into the Internet of Things, repair on-board hardware and care for the mechanical functionality of hybrid, electric and combustible engines.”
Opportunity-related openings for youth
All of these opportunity-related openings – and there are many others – are making the Canadian automotive industry increasingly attractive to the younger generation, mounting numbers of whom are inspired by the chance to work at the forefront of automotive technology that is progressively “greener” with each passing day.
And that younger generation is refreshingly inclusive, showing interest not only in STEM roles but within the discipline of skilled trades.
The Canadian federal government stands behind this encouragingly democratic trend, which is increasingly influencing the youth of this country to consider entry into an industry many of them have traditionally ignored. To quote from Policy Options again:
“As the Canadian government sets its sights on innovation through all that is high-tech, it is important to recognize that Canada’s skilled trades people, apprentices and the institutions they train at (particularly Canada’s leading institutes of technology, polytechnics and colleges) are already on board, operating at the forefront of technology.
When the government is talking about innovation (and building the skills for innovation), skilled trades people – and the apprentices who will be the trades people of the future – must be included in the conversation. Technology’s impact on industry is undeniable and the trades are no exception. In a multidisciplinary world, increasingly dependent on science, technology, engineering and math (STEM), that is especially true.
To cope with technology’s impact, those in the skilled trades are adopting models of lifelong learning that merge the technical, the technological and the mechanical; the toolbox of today is brimming with technology and so are the classrooms in which apprentices train.”
The emerging impact of micro-credentials
An increasingly important aspect of this model of youth oriented lifelong learning is contained in a single, simple idea: micro-credentials.
Micro-credentials are rapid training programs offered by colleges, universities and indigenous institutes to help people retrain and upgrade their skills to find new employment. As reported in Manufacturing Automation last year:
“The Ontario government is investing $9.3 million in 11 training projects to help approximately 2,000 students and job seekers prepare for auto and advanced manufacturing careers. The funding will support projects from a range of organizations, including auto manufacturers, industry associations, training providers and public universities and colleges.
The training projects range from hands-on learning opportunities for students in co-op or internship settings to short-duration college courses that help laid-off workers learn to operate high-tech machinery or gain credentials for jobs in the auto or advanced manufacturing sector.”
What follows are just a few of the Ontario automotive industry micro-credential initiatives currently planned or underway:
Automotive Parts Manufacturers Association (APMA): $2,242,337 to create up to 669 hands-on learning opportunities in the auto sector for college and university students, graduates and apprentices across Ontario.
Stellantis – Fiat Chrysler Automobiles (FCA): $480,000 for the FCA Canada Student Employment Experience. It will create up to 160 hands-on learning opportunities in research, production and office roles for students in Windsor, Brampton and Etobicoke.
George Brown College: $2,521,352 for their Drive Ability – Opening Doors Program, which aims to create up to 600 hands-on learning opportunities for college and university students and establish a talent pipeline for the automotive and advanced manufacturing sector. George Brown College is partnering with five public colleges and York University on this work.
Skills for Change of Metro Toronto: $504,000 for their Welding and Employment Skills Training Program. This project will help up to 24 laid-off, at-risk or under-utilized auto or advanced manufacturing workers gain a new credential and transition to other roles or sectors within the auto or advanced manufacturing industry.
Ford Motor Company of Canada: $954,324 to create up to 244 co-op learning opportunities that prepare college and university students for the fields of advanced manufacturing, vehicle connectivity and business operations.
Canadian Skills Training and Employment Coalition (CSTEC): $791,429 to create up to 180 hands-on learning opportunities with automotive employers for college and university students.
Centennial College: $871,429 for their Advanced Manufacturing & Automation Technology Experiential Learning Initiative to create up to 200 hands-on learning opportunities for college and university students and prepare them for careers in the automotive sector.
While the foregoing numbers are relatively small in net terms, they speak to an emerging employment trend in the automotive industry – one we can all applaud.
Conclusion
All of this plays positively into the findings of the FOCAL Initiative’s most recent Automotive Industry Labour Market Analysis: Youth Employment in Canada’s Automotive Industry which explains that:
- Ontario accounts for approximately 86% of automotive employment in Canada and Québec accounts for about 8%.
- Both provinces will experience significant shifts in the age distributions of their populations over the next decade.
- This will place increased pressure on automotive manufacturing employers as they attempt to attract young people as new employees.
A combination of rapid and accelerating technological innovation, pro-active government support and demographic reality is making youth opportunities in Canada’s automotive sector increasingly compelling. Taken together, they constitute an important and necessary new potential talent pipeline for our industry.
Find out more from FOCAL
The Future of Canadian Automotive Labourforce (FOCAL) Initiative is a collaboration of the Canadian Skills Training and Employment Coalition (CSTEC), the Automotive Policy Research Centre and Prism Economics and Analysis.
Funded by the Government of Canada, you can find out more about us on our website and follow us on Social Media – LinkedIn, Facebook, Instagram and Twitter – and through our newsletter.